Kyle has graduated from apprentice to novice carpenter. He created this video to document his first major solo woodworking project. With new tenants about to rent his newly renovated basement, he decided to add much-needed storage to his garage in the form of 2-foot-deep shelves. It fills me with great joy to see him using the skills he developed while we worked together on the renovation.
Monthly Archives: June 2023
House Numbers
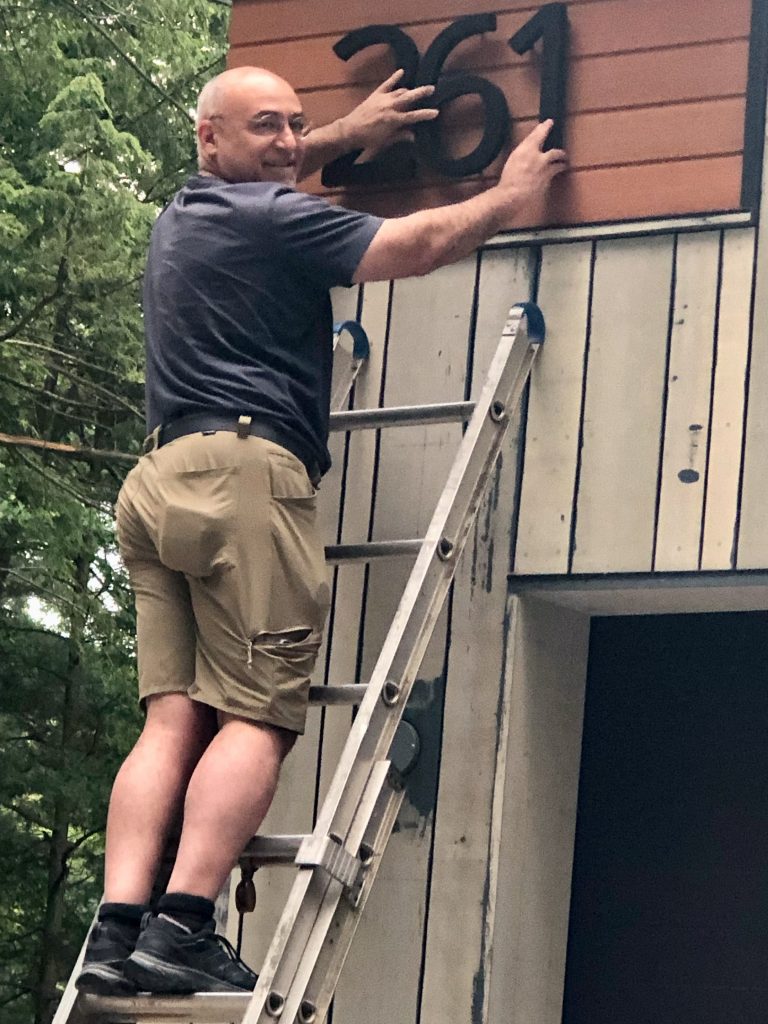
Jeanine joined me at the River House to check out the build progress. We used the opportunity to model what our house number will look like at scale. Maya 3D printed these numbers for us at work and even though I could not hold them up with the proper spacing, we are very pleased with the size. Initially, we thought we would buy backlit numbers and I provisioned for the power to do this. Upon further reflection, however, I think we have decided that we would prefer not to illuminate the numbers. Visitors looking for our house at night will be more likely to rely on the reflective numbers on our mailbox than peering through the 300 feet deep forest of trees separating our house from the road.
Turtlecide
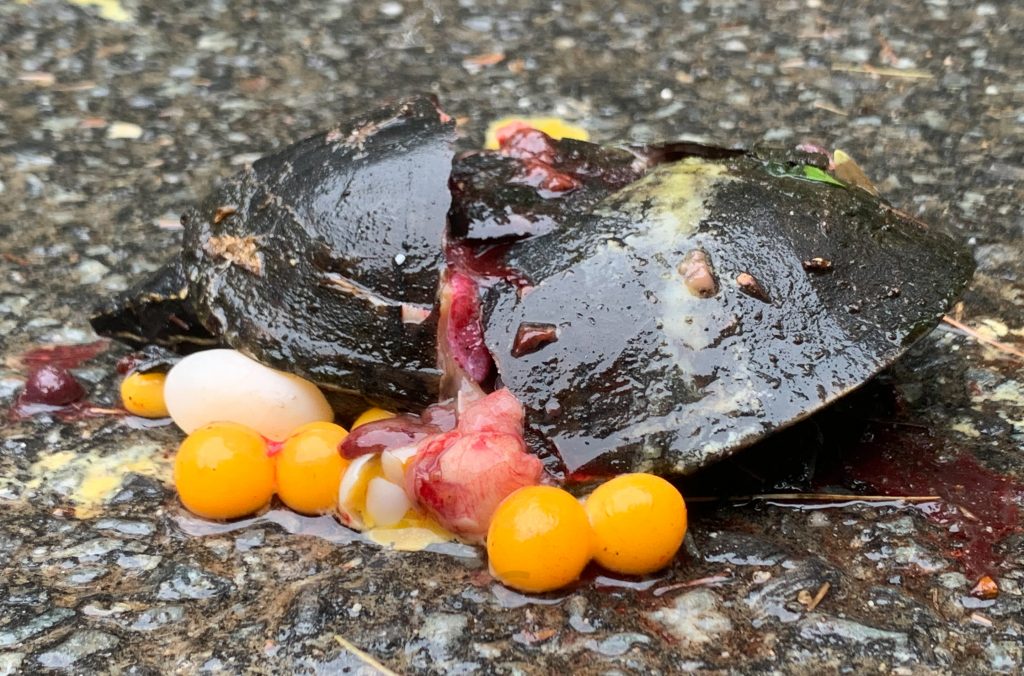
Last weekend I ran over a turtle with my car when I arrived at the River House to work. It would appear to be a female snapping turtle and measured about 7 inches in length. I did not see the turtle nor did I realize I had driven over it. I only noticed it when I got out of my car and immediately felt sick to my stomach, not at the sight, but because I had caused the death of this wonderful creature. I suspect the turtle had come from the river in search of a place to bury her eggs. This only compounded my feelings of guilt. By the time I had completed my work for the day, all that remained of the turtle was its shell. I take a small measure of consolation knowing that the other wildlife we share our yard with gained nourishment from this tragedy. Over the course of my life, I have helped to save a handful of wayward turtles. I hope this history of compassion and care will help me to forgive myself.
The Cutting Edge
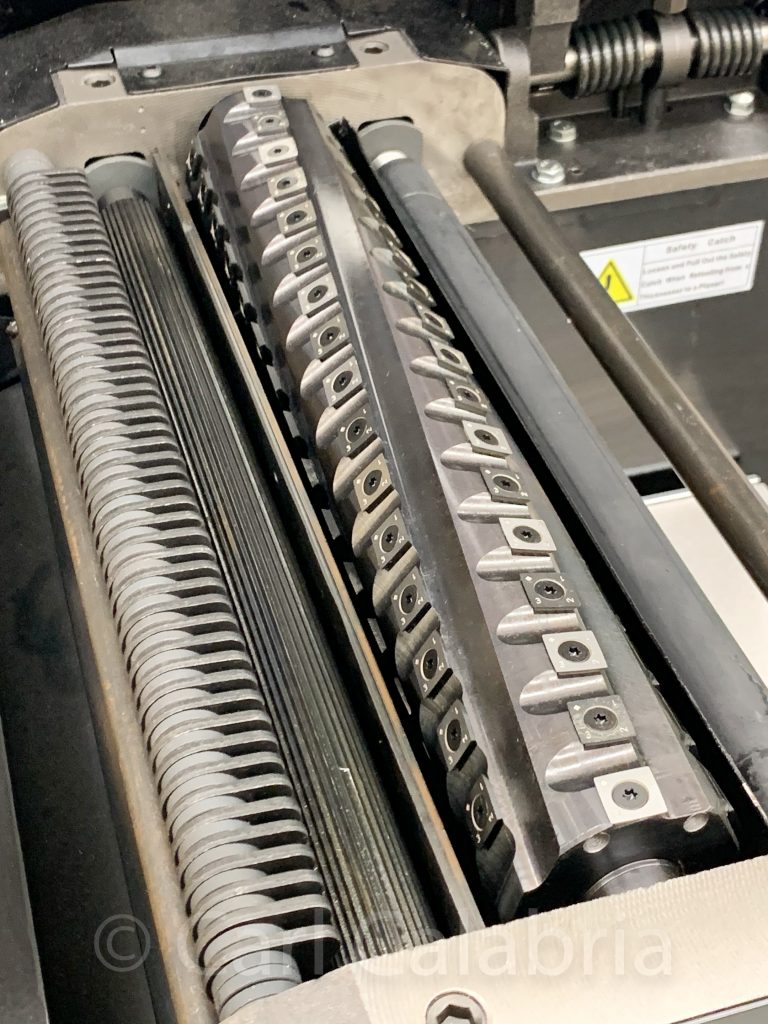
My new jointer planer has 5 rows of 15mm x 15mm x 2.5mm square four-sided convex edge carbide knives for a total of 80 knives. When an edge of a knife gets dull or damaged you simply remove the locking screw and rotate the knife to a new edge. The helical arrangement of the blades results in a smoother cut and less tear-out on difficult grain. I spent some time doing the final tuning of the infeed and outfeed tables today as well as sealing all the joints on my dust collection system.
Open For Business
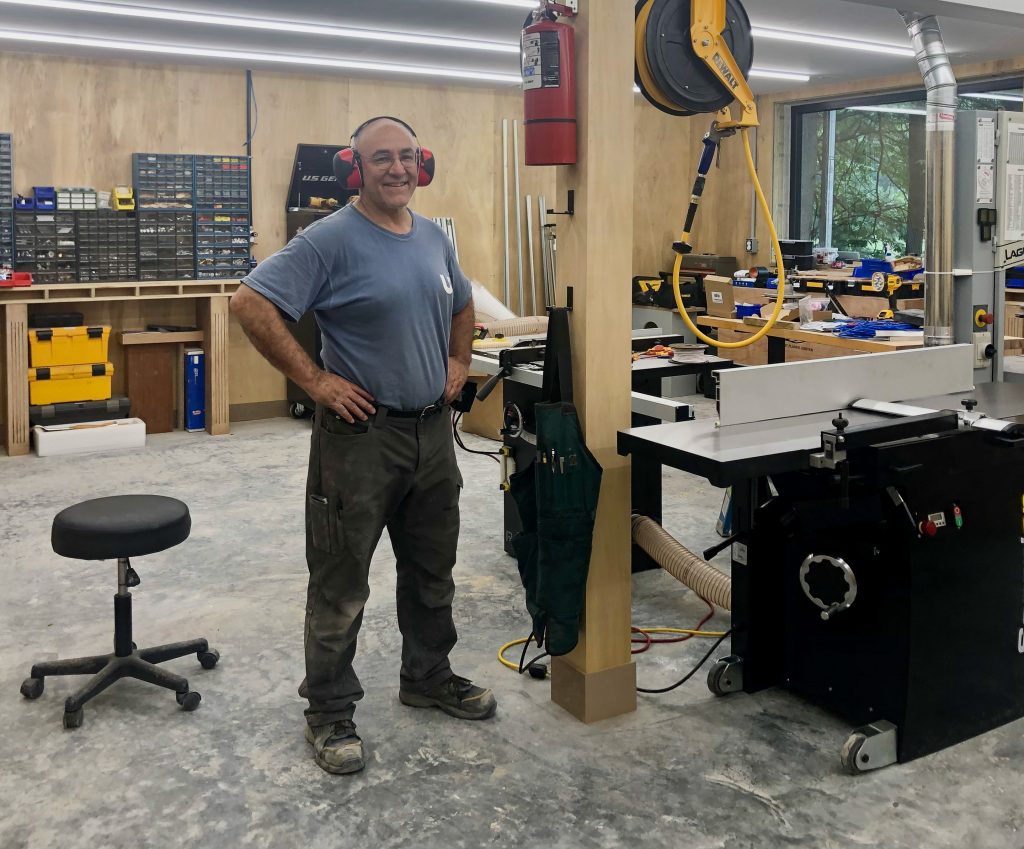
While it is far from complete, my new wood shop at the River House is officially open for business. As of today, all of my major machines are operational and I have access to most of my tools and building supplies. The automatic dust collection system is up and running on my table saw, jointer/planer, and bandsaw. Jeanine stopped by to see the garage doors that were installed today and found me working in my shop for this photo. Just ten days ago, this was an empty room and now I am ready to start building cabinetry for the house.
Boston Unity Cup
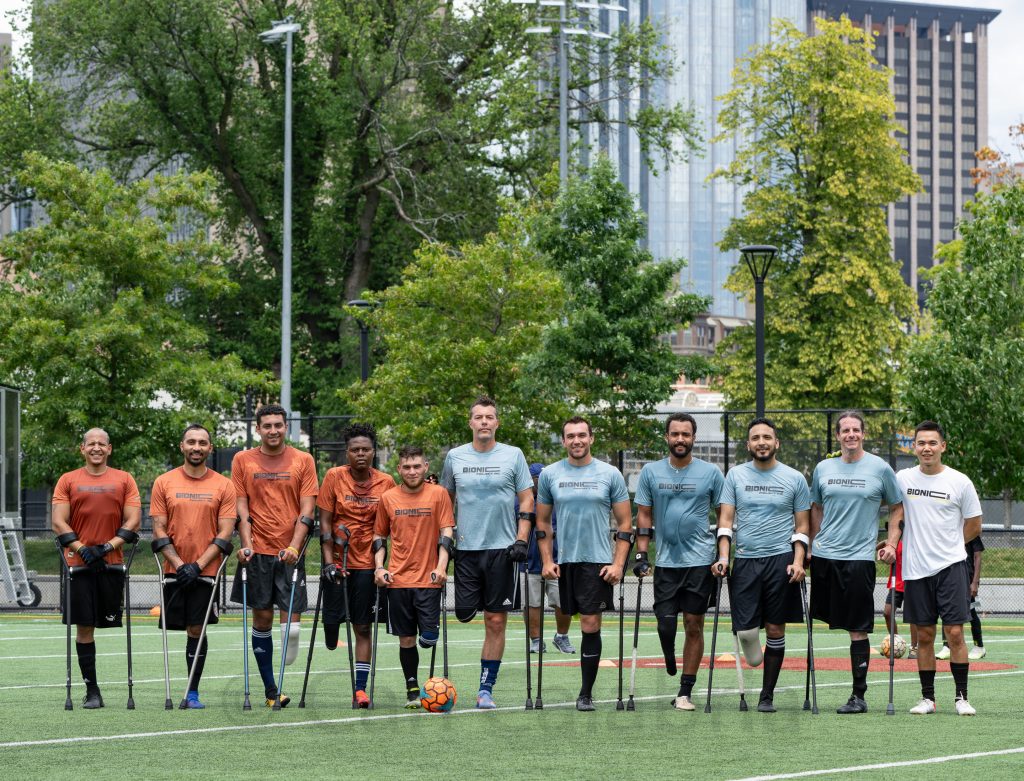
Nicolai returned to the soccer pitch this afternoon playing in a showcase match to kick off the month-long Boston Unity Cup. He played with and against many of his teammates from the US national team as well as several exciting new players who have recently joined the sport. The tournament is meant to reimagine the power of soccer to build community, connect people from diverse backgrounds, and promote equity. Nico had 2 goals and 2 assists in a tight 4-3 win. Photos from the match can be found here.

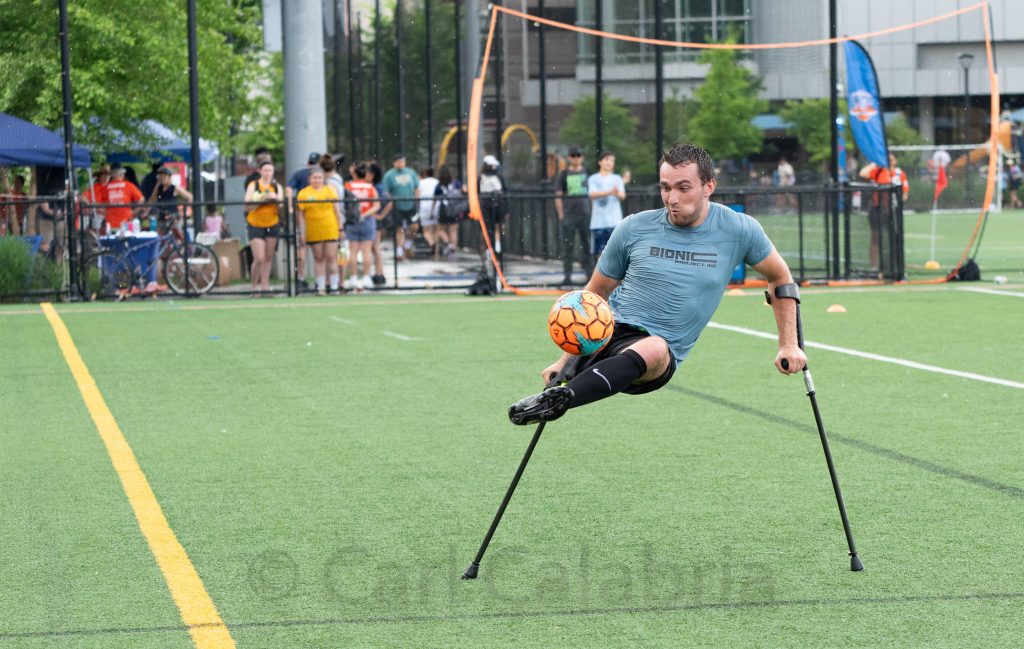
Consolidation
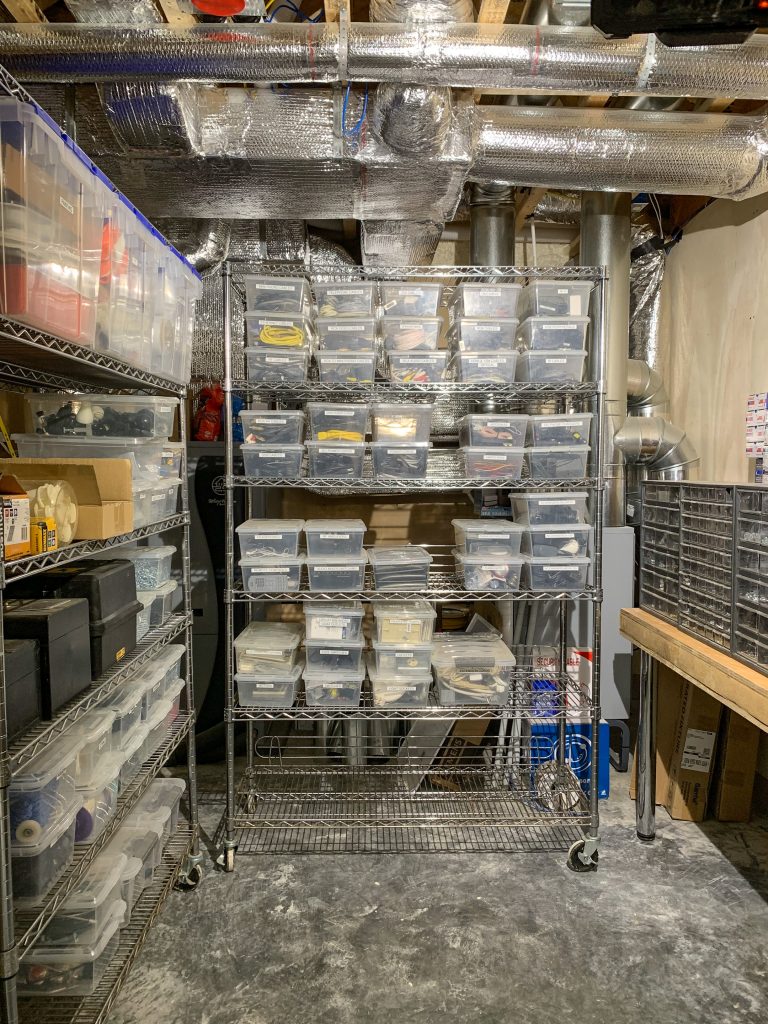
I spent the morning moving tons (literally) of shop supplies and hardware from the detached garage where it has been stored for the last two and a half years into the new house’s basement. A constant light rain only added to the drudgery of the task. Currently, the mechanical room and shop are the only two rooms that are ready for occupancy, all others have yet to be painted. As I have yet to create any permanent storage solutions in the shop it is getting quite crowded so I opted to temporarily store much of what I moved in the mechanical room.
Having successfully tested my first pneumatic blast gate earlier in the week, I moved on to the assembly and testing of the remaining units during the afternoon. I still have to fabricate and attach the arm that connects the pneumatic cylinder’s piston to the blast gate.
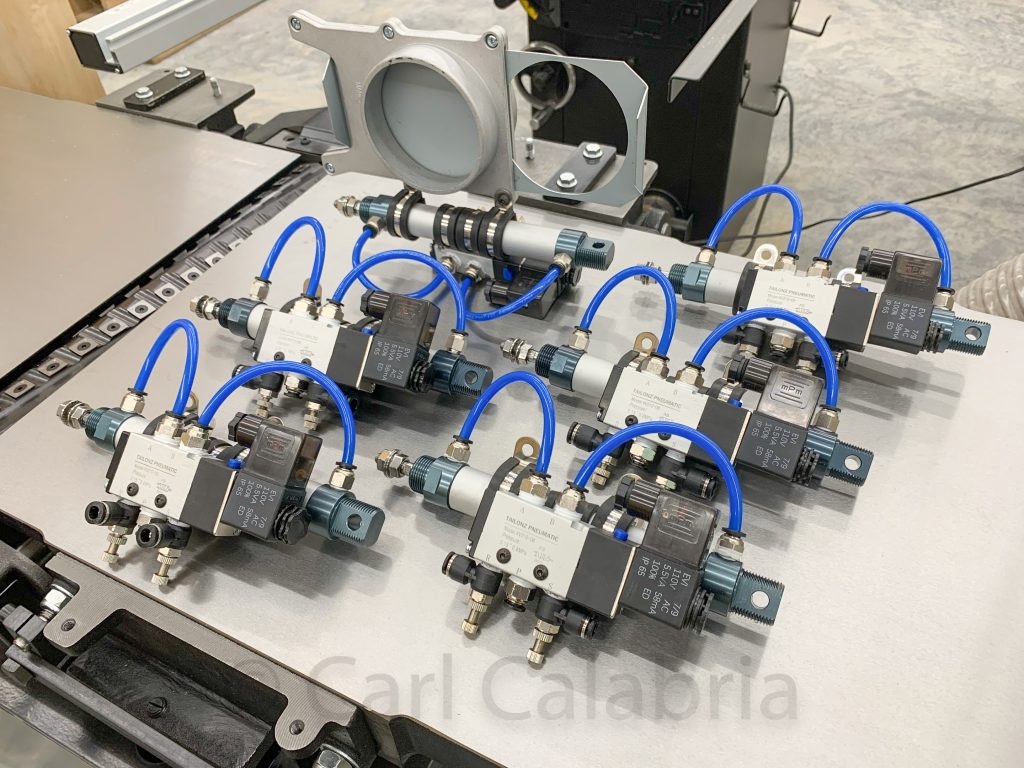
Having a Blast
The dust collector in a wood shop is a shared resource. In the simplest systems, you connect a single hose to whichever machine you happen to be using. This stops being fun on your first project. The next step up incorporates an array of ducts that connect all machines to the dust collector. This requires “blast gates” at each machine so that only the one being operated is open thus maximizing air flow. This is what I have used in all my previous shops. Whenever you move to a new machine, you close the blast gate of the last machine and open the blast gate of the next machine. Over the years, this too becomes tiresome. The ultimate solution is an automated system that detects which machine you are using and opens only the blast gate connected to it and turns on the dust collector. A couple of years ago, I design such a gate fashioned from an off the shelf blast gate coupled to a pneumatic actuator and control valve. This afternoon, I connected the first of seven to my bandsaw. Open and close times are fully adjustable. I plan to slow the close enough to allow the dust collector to clear the ducts before shutting down.
Moving Heavy Things Day
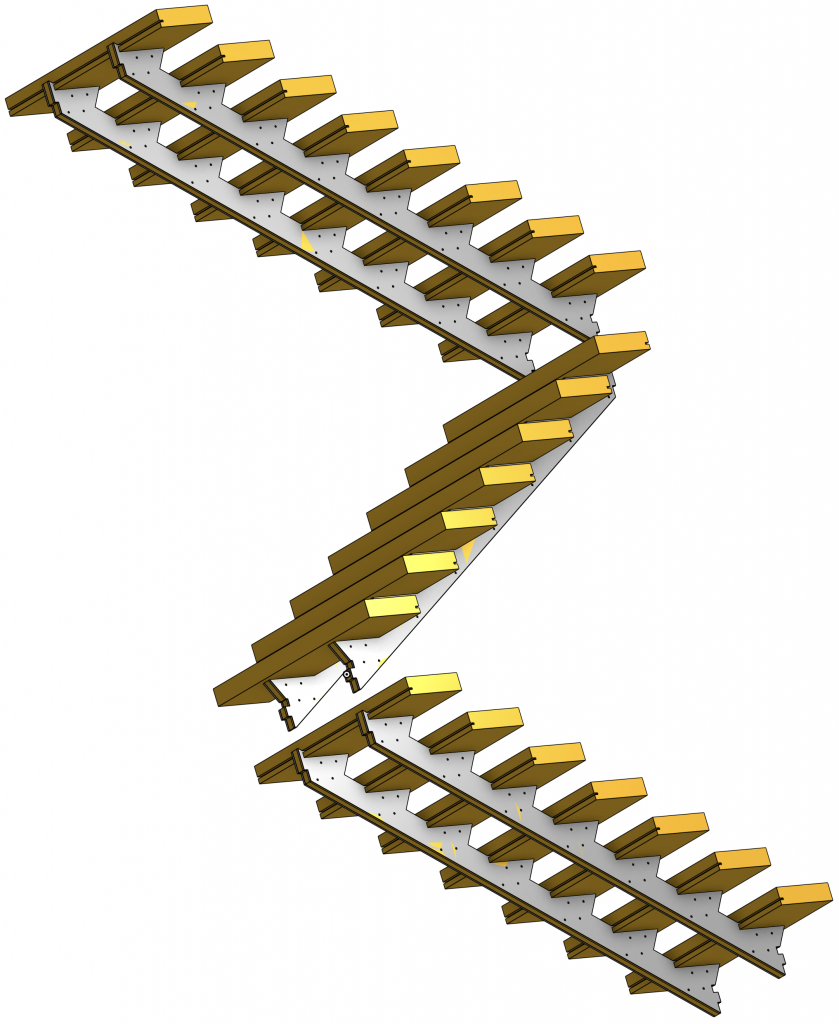
For the second time this week, I rented a trailer from U-Haul. This time it was to pick up 780 pounds of laser-cut steel stair stringers that we will be using in the River House. Pictured above is a photo from earlier this month depicting my final design. Below are the fabricated stringers loaded onto a utility trailer. On and offloading these was quite a good workout with each of the twelve averaging 65 pounds.
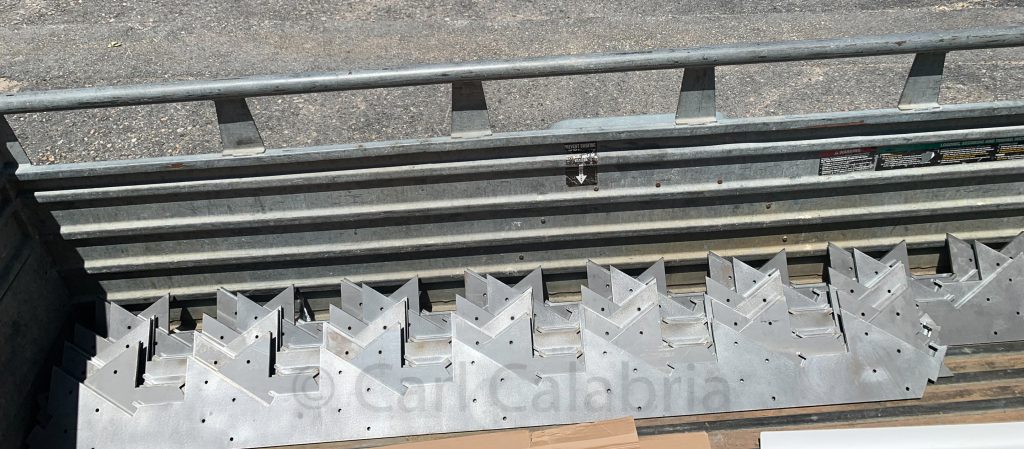
As if I needed more exercise, I decided that today was the day to move my very heavy jointer/planer from the garage into my shop. The ground was relatively dry and weather predictions are calling for on-and-off rain for the next several days. Using a bunch of blocks and levers, I single-handedly got the machine off its shipping pallet and onto the dolly I built yesterday. I was grateful that Kyle was able to join me after he finished work to assist with the difficult task of getting it down to the basement level and up a home-built ramp onto the shop floor.
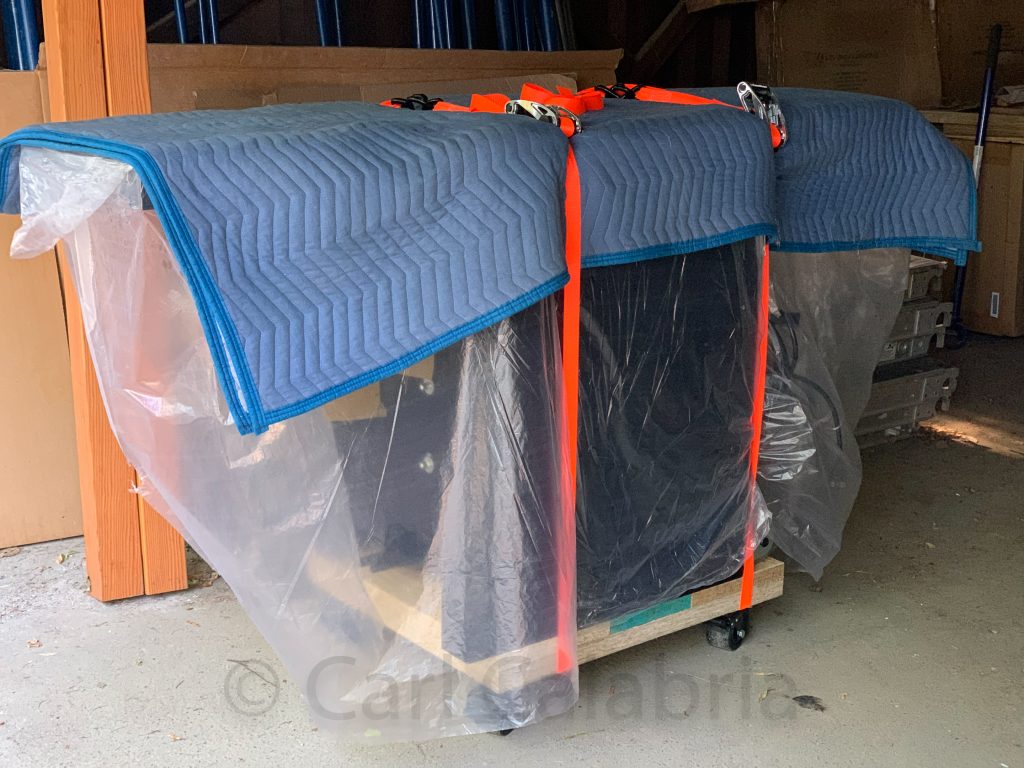
Two Ton Dolly
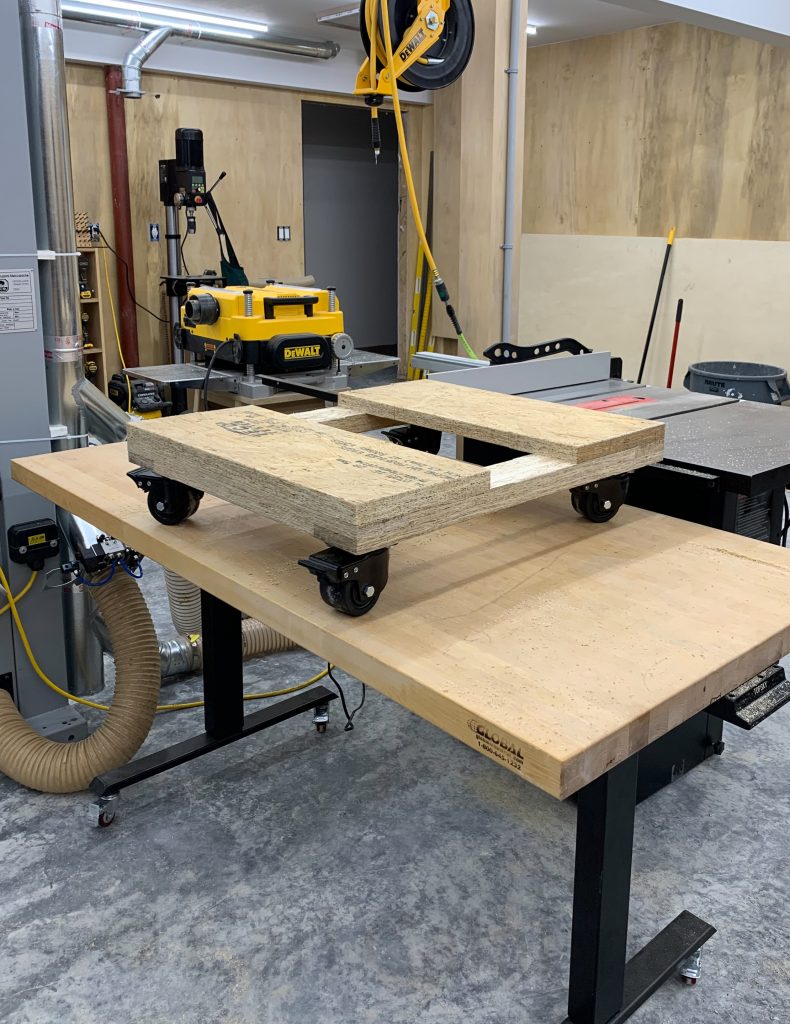
I have decided that the best way to move my nearly 600-pound jointer/planer from the garage where it is currently stored into the shop is with a dolly and a couple of strong helpers. I looked at purchasing one but was put off by the price. Cheap ones with a 2x safety factor are around $300 and from their appearance do not seem up to the task. Really well-designed ones are almost twice that much. I decided to pick up a set of swivel casters rated for an 1100-pound load each ($60 for the set) and built the base out of left-over framing lumber. The wheels are 4 inches tall and 2 inches wide. I plan to use scrap sheets of OSB for a smooth surface over which to roll the loaded dolly. Only time will tell if this plan works out. Of one thing I am certain. This dolly will definitely stand up to the load.
Side Note: My shop is now largely operational. I used my miter saw, table saw, bandsaw, and planer in the construction of this project which features lap joints at the corners.
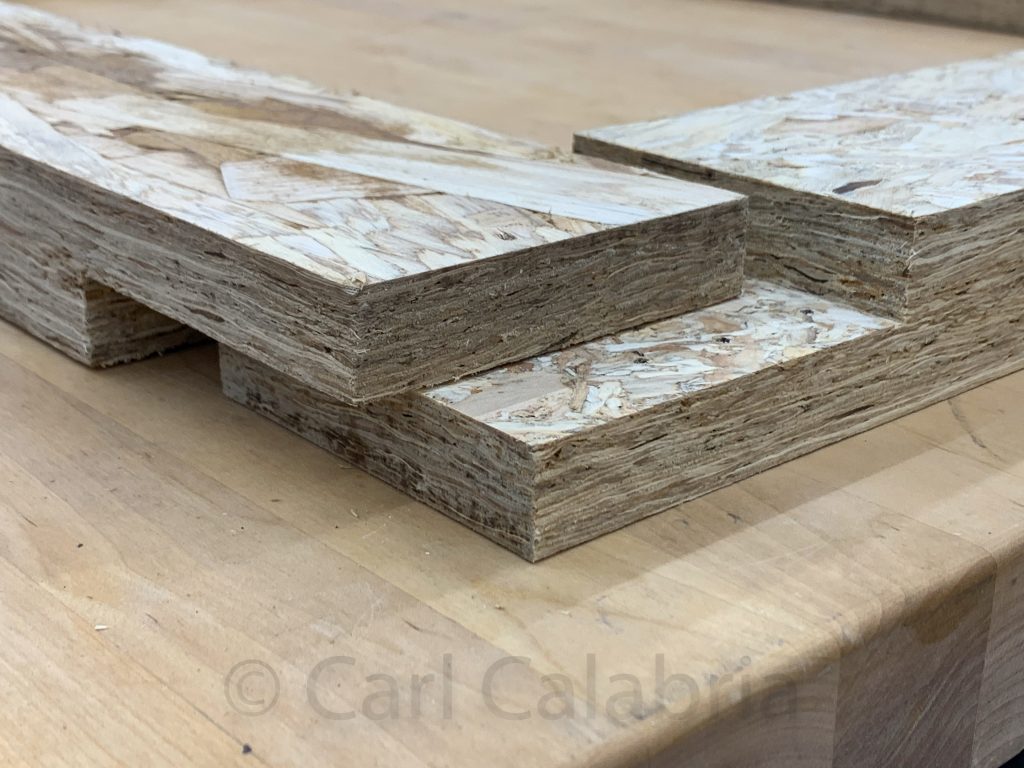
Huevos Rancheros
Downlights
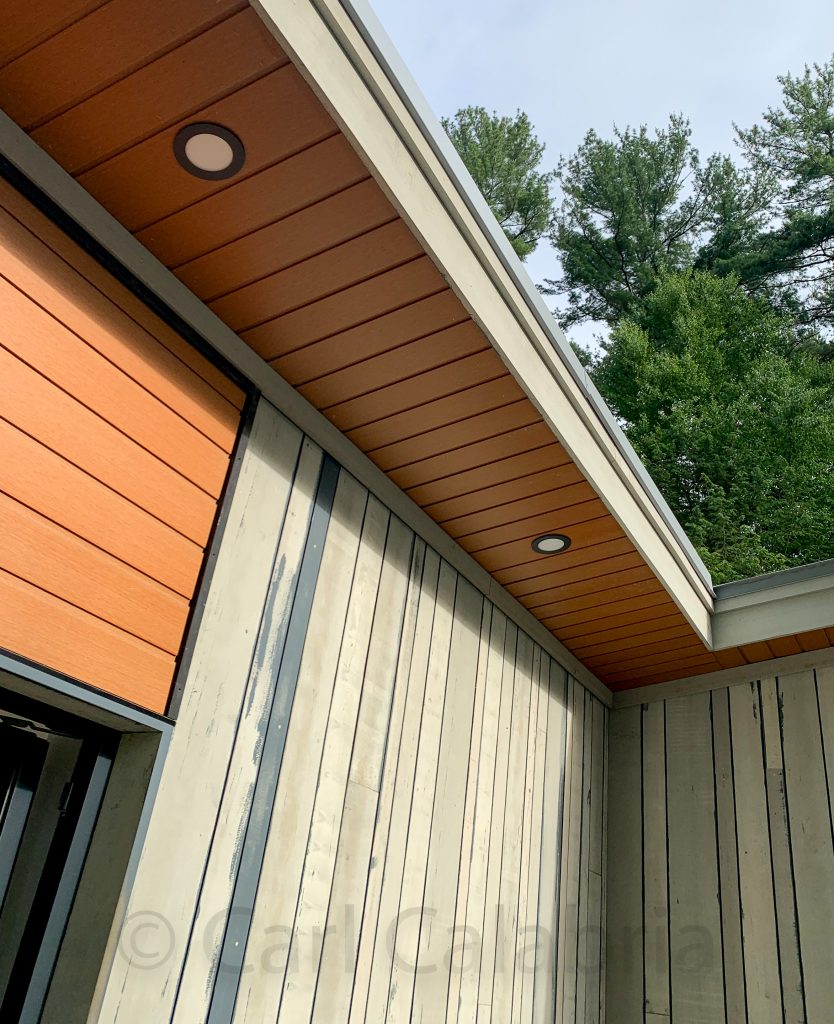
Our house builder has been making slow and steady progress on the soffits. They are using a man lift to position themselves under the eves to facilitate the work. Before moving it to a new section of the roof, I hitched a ride to install the downlights that will illuminate a future patio. Beats the hell out of a ladder.
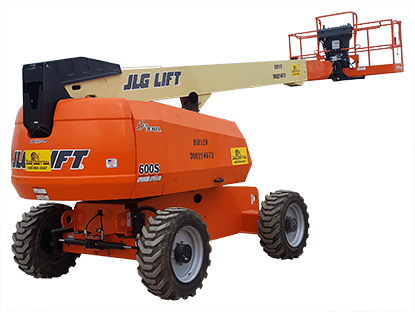
Nephew Visit
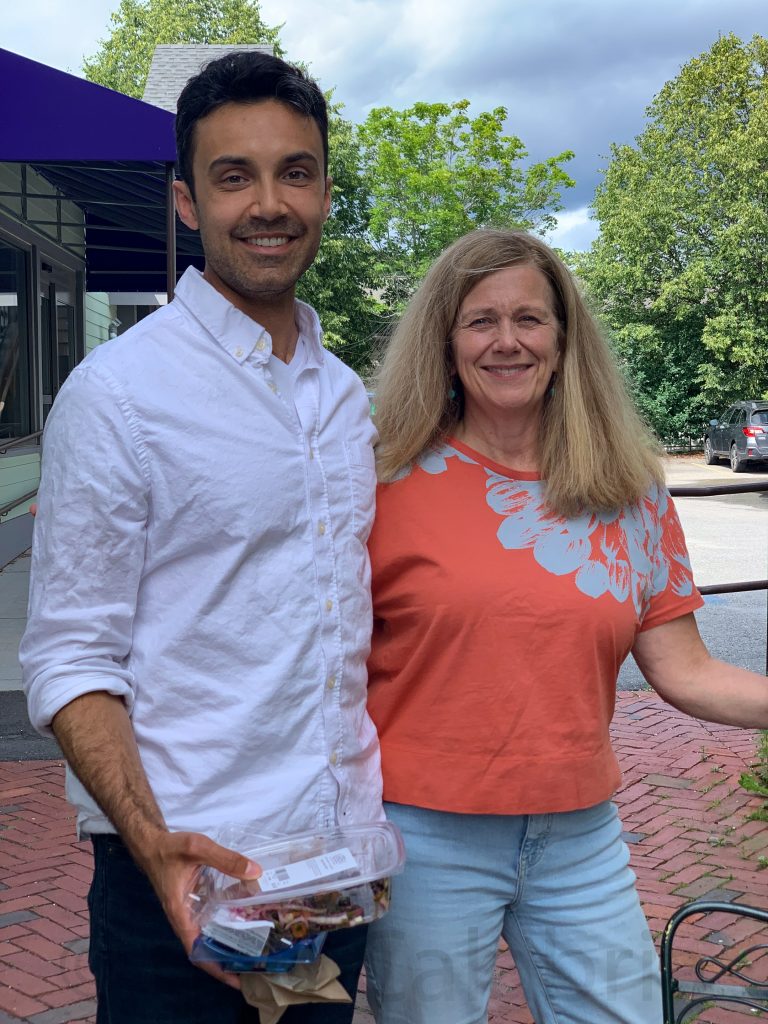
We enjoyed a visit today from our nephew, John Quinn. He met us at the River House for an extended tour followed by a late lunch in West Concord. It was great to catch up with him and learn about his plans for the future.
I spent the balance of the day moving into and beginning to organize my new shop. Tomorrow, I plan to install provisional dust collection and will be very nearly ready to start cabinet making once the bamboo plywood I ordered arrives.
Strawberry Festival
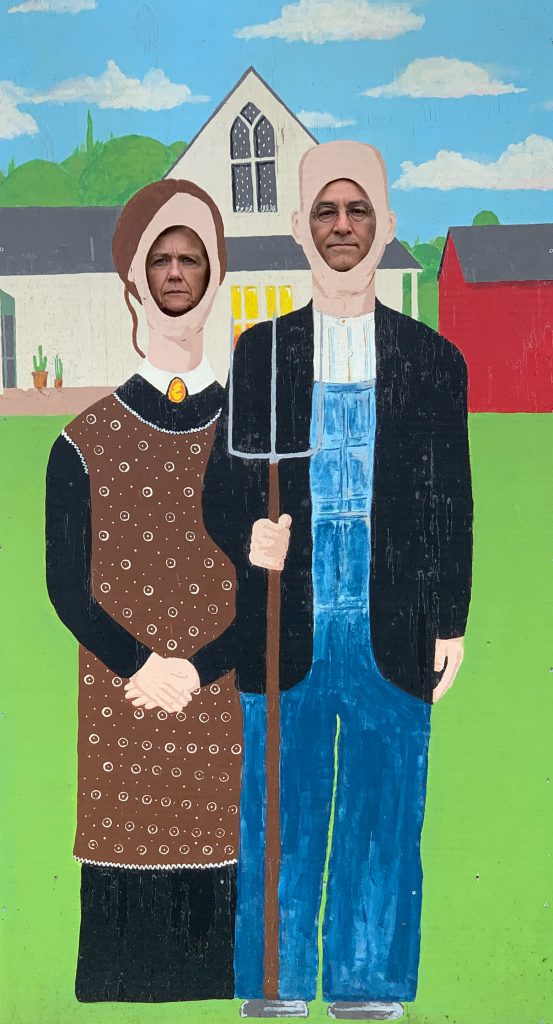
Today, we celebrated both Father’s Day and Maya’s birthday, one and two days early respectively. We attended the Verrill Farm Strawberry Festival in the morning and were fortunate to miss the rain that fell for much of the rest of the day. Jeanine suggested the event and I thought it would be great fun. After noticing the very large number of small children in attendance, Kyle suggested this was a planned attempt to accelerate the timetable for having grandchildren. No such subterfuge was at play but if it had that effect, I will be choosing to attend the festival again next year. I feel very fortunate that the kids all live close by and that we can be together so often.
In the afternoon, Kyle helped me to collect a three-piece recliner that will go in the mini-theater of our new house. While we had the U-Haul trailer we also returned the recliner that Jeanine has been using while recovering from her foot surgery and moved a bunch of shop equipment from the Road House basement to the River House.
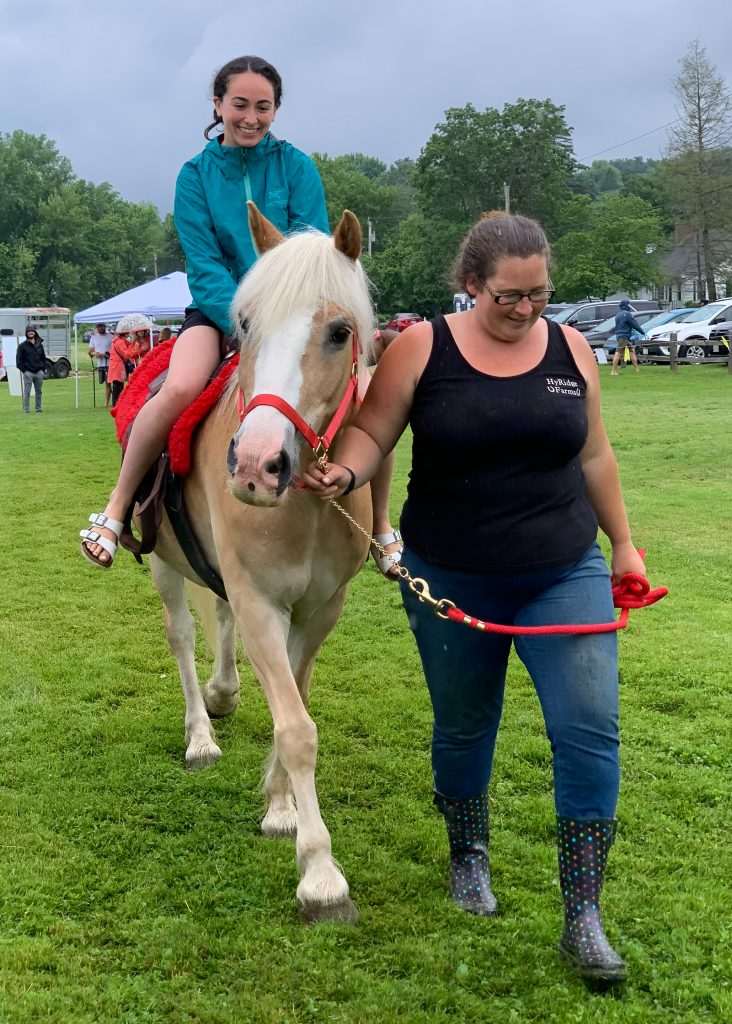
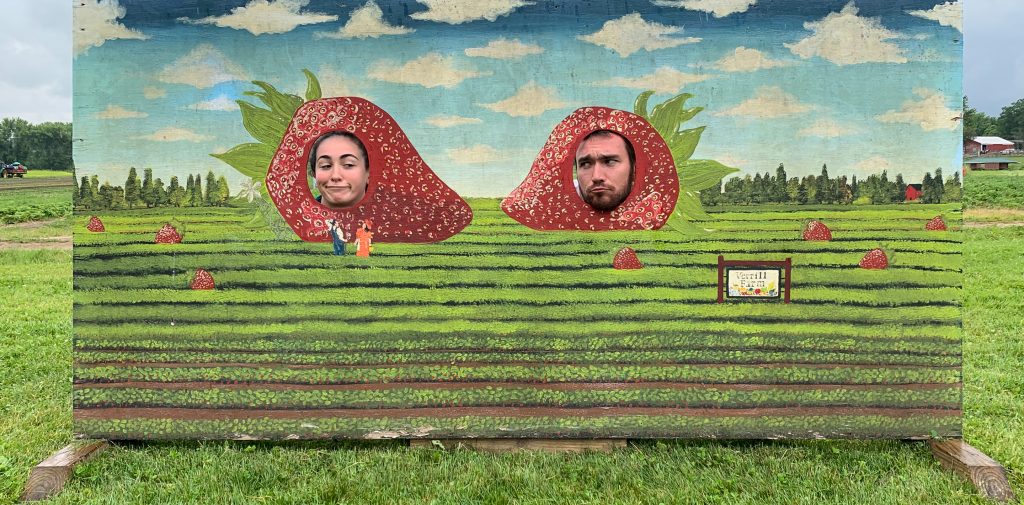
Let There Be Light
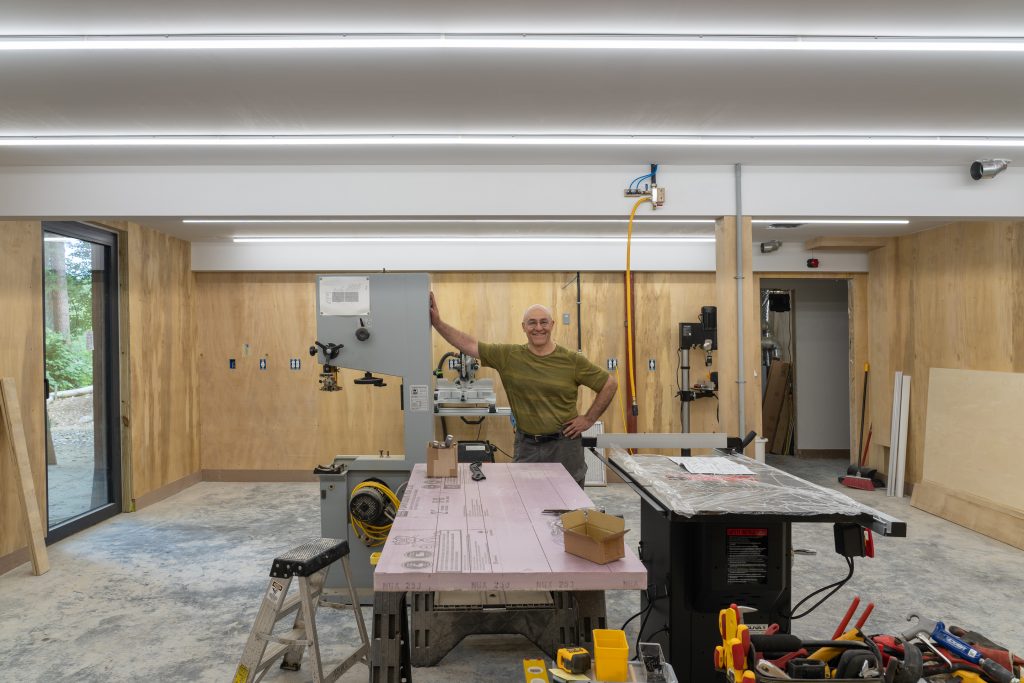
This morning, I installed lighting for my new shop. The setup includes 7 rows of 20-foot-long linear LED lamps. Each 20-foot section is made up of five 4-foot-long sections (four rows are visible in the photo). The total light output is 75,000 lumens. The arrangement provides shadow-free very bright illumination over the entire shop. When full brightness is not required, only half the lights can be turned on but still cover the entire floor space.
In the afternoon, I moved my table saw and bandsaw from the garage into the shop. I managed the effort single handed but will need help with the jointer/planer which weighs twice as much at 572 pounds. Once I lock in the location of each machine, I will connect each to my dust collection system and will declare my shop open for business. That business will include making all the kitchen cabinets and vanities for all the bathrooms.
4 Weeks and Crutching
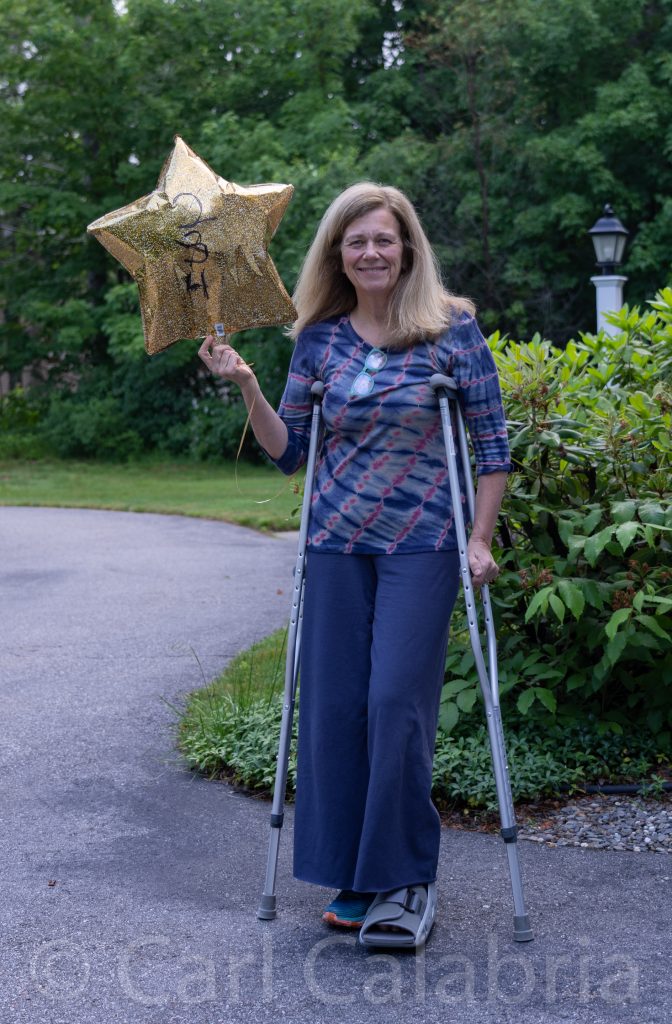
It has been 4 weeks since Jeanine had foot surgery to correct a previously botched bunion procedure. Her doctor has given her the all-clear to start putting up to 50% of her weight on the foot. Although her knee scooter is still the most comfortable way to move around, the process of loading and unloading it from the car has kept her from driving anywhere. Now that she is up on crutches, she is back on the road again.